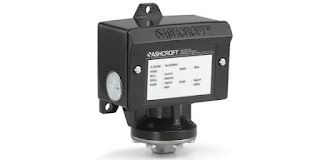 |
Electronic pressure switch in NEMA 4 enclosure.
Image courtesy of Ashcroft |
A
pressure switch is a device that detects and responds to fluid pressure. Pressure switches use a variety of sensing elements such as diaphragms, bellows, bourdon tubes, pistons or electronic sensors. In all but the electronic sensor versions, the movement of the sensing element, caused by pressure fluctuation, is transferred to a set of electrical contacts to open or close a circuit. Electronic pressure switches utilize a sensor signal and circuitry to control switch activation.
The normal status of a switch is the resting state with stimulation. A pressure switch will be in its normal state when low or minimum pressure is applied. For a pressure switch, normal status is any fluid pressure below the trip threshold of the switch.
One of the earliest and most common designs of pressure switch was the bourdon tube pressure sensor with a mercury switch. When pressure is applied, the bourdon tube flexes enough to tilt the glass bulb of the mercury switch so that the mercury flows over the electrical contacts, thus completing the circuit. the glass bulb tilts far enough to cause the mercury to fall against a pair of electrodes, thus completing an electrical circuit. Many of these pressure switches were sold on steam boilers. While they became a de facto standard, they were sensitive to vibration and breakage of the mercury bulb.
Pressure switches using micro type electrical switches and force-balanced pressure sensors is another common design. The force provided by the pressure-sensing element against a mechanical spring is balanced until one overcomes the other. The tension on the spring may be adjusted to set the tripping point, thus providing an adjustable setpoint.
One of the criteria of any pressure switch is the deadband or (reset pressure differential). This setting determines the amount of pressure change required to re-set the switch to its normal state after it has tripped. The differential pressure setting of a pressure switch should not to be confused with a differential pressure switch, which actually operates on the difference in pressure between two separate pressure input ports.
Electronic pressure switches provide some features which generally are considered advantageous to mechanical designs.
- No mechanical linkage between sensing element and switch, all electronic.
- High cycle rates are possible.
- High levels of accuracy and repeatability.
- Some models have additional features, analog output, digital display, auxiliary switches, and more.
When selecting pressure switches you must consider the electrical requirements (volts, amps, AC or DC), the area classification (hazardous, non-hazardous, general purpose, water-tight), pressure sensing range, body materials that will be exposed to ambient contaminants, and wetted materials.
Whatever your pressure measurement application, share your challenges with a
fluid measurement and control specialist, combining your own knowledge and experience with their product application expertise to develop effective solutions.