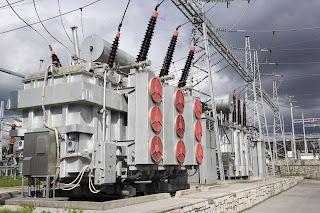 |
Continuous monitoring of remotely located
equipment yields a wide range of benefits |
Industrial operations and processes are populated with unimaginable variations of equipment and applications, each with specific operating sequences intended to produce a specific outcome. By their scale and nature, most have the capacity to substantially impact the success of the organization. As stakeholders in the operation of industrial processes and equipment, we have an interest in monitoring their performance for any number of reasons.
- Financial - The investment in plant and equipment is financially significant to a company of any size. An operator benefits from monitoring process inputs and outputs. Scrutinizing the operating status of process equipment and intermediate process conditions provides valuable information that can be used to minimize negative events of many types.
- Maintenance - Keeping a real time watch over operating characteristics of machinery can present opportunities to head off trouble before it happens. There are many warning signs that can precede equipment failure, and taking prompt remedial action requires issuance of real time warnings.
- Safety - Industrial operations of all types tend to exhibit levels of hazard to personnel or environment ranging from minor to potentially catastrophic. The rigorous procedures employed to maintain operation within prescribed limits are enabled through the use of information about process conditions.
- Regulatory - There can be jurisdictional requirements to monitor and report certain process characteristics. An ability to conduct the needed action from afar, without having to station personnel at a remote location, has some real benefit.
This list is not intended to be complete or definitive. There are countless ways that process operators can use real time data to enhance all facets of their operation. A challenge arises when the process or operation extends over a large area, perhaps beyond the boundaries of the primary facility. That's where telemetry serves as the means to deliver needed information to a decision making location.
Modern requirements for "knowing what is happening" increase the need for telemetry in industrial operations.
Telemetry is getting the information you need from a remote or inaccessible location and delivering it to where it can be used for decision making.
With the wide array of hardware offered by process measurement and control equipment suppliers, implementing the data collection and transmission has become a fairly straight forward task. Simply put, here is what you need to accomplish.
- Measure or detect the information needed. You know how to do this. Sensors, counters, or other regularly available process measuring equipment is what is needed here.
- Convert the measurement into a transmissible form. This will likely be accomplished by the transmission gear. The measurement devices you use should provide an output signal that is compatible with the input requirements of the selected transmission equipment.
- Transmit the information to the receiving station (the decision making point). The device and equipment manufacturers do most of the hard work of accomplishing this task. Generally, regardless of the transmission method, the extent of the work needed to put transmission into operation involves powering up the equipment and assigning addresses or channels to identify the source of the signal.
- Receive the signal and convert it to a form readable by the decision making portion of the system. Again, the telemetry equipment manufacturers handle the details in the design of their equipment. Implementation consists of similar steps to those of the transmission equipment.
It is recommended that the transmission method be selected first. It must accommodate any challenges presented by the distance to be covered and any obstacles that may impact the delivery of the signal to its destination. Coordinate the measuring device output signal selection with the transmission device input requirements. The receiving equipment must be capable of producing an output signal that is readable by whatever decision making or recording equipment is used.
Below is a case study illustrating how a user derived a signal from a utility plant to provide data on local power consumption.You will see how they selected and employed equipment to accomplish the four tasks outlined above.
The applications are only limited by your imagination and ingenuity. Instead of wondering about what is happening at remote locations, operators can now easily measure and deliver useful operating information across almost any distance. Share your challenges with
process control specialists and develop the solutions you need.