Many industrial and commercial liquid systems have mechanical components that cannot tolerate particulate matter in the liquid. Pumps, valves, sensors, and other specialties can experience accelerated wear and tear due to certain types and sizes of particulate matter.
Good practice dictates that the tolerance of the system for particulate matter should be determined and a properly sized and configured device be put in place to remove particulates larger than greatest allowable size. Considerations for connection size and type, construction material suitability for the process media, flow rate, pressure drop, and filter holding capacity should all be a part of the product selection criteria.
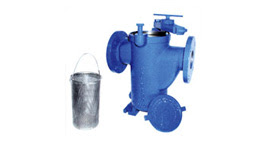 |
Simplex basket strainer with access cover and basket removed Courtesy Eaton Filtration |
One key element of the selection criteria is whether the system can be temporarily shut down for replacement or cleaning of the filtration element. A basket strainer, one of several types of liquid filtration devices, is available in both simplex and duplex variants. A simplex basket strainer functions as a single unit, requiring flow stoppage when the basket becomes clogged with debris. The changeover time may not be long, but some processes cannot tolerate any downtime. A duplex strainer is comprised of two simplex strainers, incorporated into a common housing, with an inlet chamber and diverting valve that selects which strainer basket will process the liquid flow. Changes in pressure drop through the device can be used to signal when it is time to switch operation between the strainer baskets.
Fluid filtration can be an important part of keeping a process in operation, reducing wear and tear on piping system components and equipment. Share your process fluid filtration challenges and requirements with
application specialists, combining your process knowledge and experience with their product application expertise to produce effective solutions.