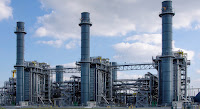 |
Reducing costs at power plants. |
For most power plant operators, fuel expenditures account for seventy to eighty percent of production costs and millions of dollars per year. In fact improving heat rate one percent could generate five hundred thousand dollars an annual savings for five hundred megawatt power point.
To contain fuel costs, power plants must maximize the efficiency of their feed water heaters. That's why many companies today are focusing on improving heat rate as a way to use their feed water heaters more effectively, and significantly reduce their fuel costs.
Heat rate is a measure of how efficiently a power plant uses heat energy. You can measure heat rate by the number of BTU’s your plant requires to generate a kilowatt hour of energy. As you're heat rate goes up so do you're fuel costs.
The condenser is the beginning of the feed water heaters process, where condensed steam from the feed water heater drains, and HP, IP and LP turbines is routed through successive feed water heaters. At the same time, extractions steam from your turbines reaches the appropriate feed water heaters and the transfer of energy takes place.
Maintaining
accurate and reliable level control throughout this cycle is critical to achieving the final feed water heater temperature that your process requires.
Let's take a closer look at how this works. Feed water heaters use the heat of condensation to preheat water to the correct temperature for the boiler. During this process, shell and tube heat exchangers allow feed water to pass through the tube side and extract steam from the turbine to the shell side.
The primary benefit of this process is that the feed water heater decreases the fuel costs by using recovered energy, rather than costly hot gas, to heat the water.
Achieving optimum water level in a feed water heater is a critical component of maximizing energy transfer and minimizing controllable losses.
There are normally six to seven stages of feed water heating. Making an investment in level control can help you achieve optimum heat transfer and improved terminal temperature difference to provide a significant return on investment.
 |
Guided wave radar
transmitter
(courtesy of
Magnetrol) |
With a guided wave radar level control, you can optimize the condensing zone of your feed water heater to deliver accurate level control, maximize energy transfer, and minimize undue wear and tear. This can help you generate the savings needed to recover your investment.
Older level technologies, such as differential pressure, magnetostrictive, or RF capacitance and torque tubes are vulnerable to process conditions and induced instrument errors, such as shifts in specific gravity and mechanical or electronic drift.
In contrast, guided wave radar provides a truly reliable level measurement solution for feed water heaters. Guided wave radar performance is virtually unaffected by process variations and gives you a superior degree of accurate and reliable continuous level measurement without the need for calibration or gravity corrections.
With superior signal performance and advanced diagnostics, guided wave radar delivers premier level control for feed water heaters, as well as a broad range of challenging applications, such as condenser hot wells, deaerators, and cooling tower basins.
Combining a magnetic level indicator with guided wave radar merges the operating systems of a conventional flowed base magnetic level indicator with a leading edge solution. This allows you to effectively measure low dielectric media, high temperature, and high pressure process conditions and media, with shifting specific gravity and dielectric values accurately and repeatedly. The result is a diverse and redundant level measurement solution in a single chamber design.
For more information contact:
M.S. Jacobs and Associates
Phone: 800-348-0089
Fax: 412-279-4810
Email:
msjacobs@msjacobs.com
www.msjacobs.com