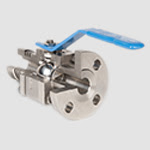 |
Industrial Ball Valve Courtesy Marwin Valve |
Oxygen is used extensively throughout a wide range of industrial processes. Medical, deep-sea, metal cutting, welding, and metal hardening are a few examples. The steel industry uses oxygen to increase capacity and efficiency in furnaces. As a synthesis gas, oxygen is also used in the production of gasoline, methanol and ammonia.
Odorless and colorless, oxygen is concentrated in atmospheric air at approximately 21%. While O2, by itself, is non-flammable, it vigorously supports combustion of other materials. Allowing oils or greases to contact high concentrations of oxygen can result in ignition and possibly explosion. Oxygen service preparation of an industrial valve calls for special cleaning processes or steps that remove all traces of oils and other contaminants from the valve to prepare for safe use with oxygen (O2). Aside from the reactive concerns surrounding oxygen, O2 preparation is also used for applications where high purity must be maintained and valves must be free of contaminants.
Gaseous oxygen is noncorrosive and may be used with a variety of metals. Stainless steel, bronze and brass are common. Liquid oxygen presents unique challenges due to cryogenic temperatures. In this case, valve bodies, stems, seals and packing must be carefully chosen.
Various types of valves are available for oxygen service, along with a wide array of connections, including screwed, socket weld, ANSI Class 150 and ANSI Class 300, DIN PN16 and DIN PN40 flanged ends. Body materials include 316 stainless steel, monel, bronze and brass. Ball and stem material is often 316 stainless steel or brass. PTFE or glass filled PTFE are inert in oxygen, serving as a common seat and seal material employed for O2 service.
Common procedures for O2 service are to carefully deburr metal parts, then meticulously clean to remove all traces of oil, grease and hydrocarbons before assembly. Valve assembly is performed in a clean area using special gloves to assure no grease or dust contaminates the valve. Lubricants compatible with oxygen must be used. Seating and leakage pressure tests are conducted in the clean area, using grease free nitrogen. Specially cleaned tools are used throughout the process. Once assembled, the valves are tested and left in the open position. A silicone desiccant pack is usually inserted in the open valve port, then the valve ports are capped. A warning label about the desiccant pack's location is included, with a second tag indicating the valve has been specially prepared for oxygen service. Finally, valves are individually sealed in polyethylene bags for shipment and storage. Different manufacturers may follow slightly differing protocols, but the basics are the same. The valve must be delivered scrupulously contaminant free.
The O2 preparation of valves is one of many special production variants available to accommodate your special application requirements. Share your valve requirements and challenges with a
valve specialist to get the best solution recommendations.