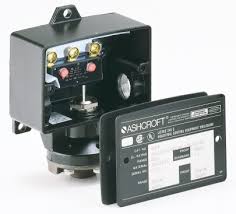 |
Internal view of pressure switch.
(Ashcroft) |
A
pressure switch is a mechanical device that detects the presence of fluid (gas or liquid) pressure. Pressure switches use a variety of sensing elements to convert pressure changes to linear movement. These sensors are known as diaphragms, bellows, bourdon tubes, and pistons. The movement of these sensors, caused by pressure fluctuation, is transferred linearly through a rod or piston to a set of electrical contacts to open or close a circuit.
The opening and closing of the electrical circuit is done through electrical contacts. These electrical contacts are most often enclosed in their own housing in an assembly known as a microswitch. These contacts in the pressure switch are associated with the terms "normal", as in "normally open" or "normally closed". The normal status of a switch is the resting state with stimulation. A pressure switch will be in its normal status when it senses low or minimum pressure. For a pressure switch, normal status is any fluid pressure below the trip threshold of the switch.
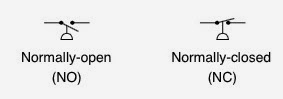 |
Switch Status Symbols |
Some of the earliest and most common designs of pressure switch was combining the bourdon tube pressure sensor with mercury switch. A bourdon tube is basically a curved tube that flexes straight when pressure is applied. The bourdon tube's flex is amplified through gearing and made significant enough to tilt the glass bulb of the mercury switch so that the mercury flows over the electrical contacts, thus completing the circuit. Many of these pressure switches were sold on steam boilers. While they became a de facto standard, they were sensitive to vibration and breakage of the mercury bulb and resulting mercury contamination.
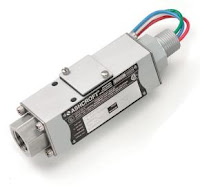 |
Explosion proof pressure switch.
(Ashcroft) |
Another common design feature pressure switches use is referred to as force-balanced pressure sensors. This design operates by countering the force provided by the pressure-sensing element with a mechanical spring. The system remains static until the pressure-vs-spring balance is overcome. Once the sensor pressure exceeds the spring tension, movement occurs and the electrical switch state is changed. In this design, the tension on the spring may be adjusted to set the tripping point, thus providing an adjustable setpoint.
Deadband or (reset pressure differential) is one of the most important application considerations when applying a pressure switch. This setting determines the amount of pressure change required to reset the switch to its normal state after it has tripped. The differential pressure of a pressure switch should not to be confused with differential pressure switch, which actually measures the difference in pressure between two separate pressure ports.
Temperature switches operate on exactly the same principle, but use the concept of thermal expansion, instead of direct pressure sensing, to create the the movement required to change the electrical contact status. In the enclosed thermal sensor (referred to as the bulb, or bulb and capillary), the liquid enclosed in the system expands and contracts in relation to temperature change. That expansion and contraction is then converted to linear movement, and then used to open and close an electrical circuit.
There are many, very important details that need to be considered when selecting and applying pressure and temperature switches. You must consider the electrical requirements (volts, amps, AC or DC), the area classification (hazardous, non-hazardous, general purpose, water-tight), pressure sensing range, temperature range, and material compatibility.
It's highly recommended you consult with a process instrumentation expert for assistance.